Motivation
Laser beam welding is significantly different from other welding processes. The special features are the high temperature gradients and the solidification rates which occur. The high cooling rates also favour the accumulation of low-melting phases in the weld, which lead to the formation of solidification cracks in the weld when critical strains are exceeded. The hot cracking phenomenon has already been investigated and described by numerous hot cracking theories and models. The existing models of solidification cracking and propagation are based on phenomenological hot cracking criteria. They use simplified material models that have only limited validity in the high temperature range and neglect many physically relevant phenomena. These factors severely limit their areas of application.
Objective
The main objective of sub-project 1 (SP1) is the development of a macromechanical FEM model to predict solidification cracking as a function of the thermal and mechanical boundary conditions during laser beam welding. A special focus is on the influence of the fluid mechanical processes in the molten pool on the resulting temperature distribution and the close-to-reality material behaviour in the two-phase and multiphase region, which have a relevant influence on the local stress and strain distribution in the mushy zone.
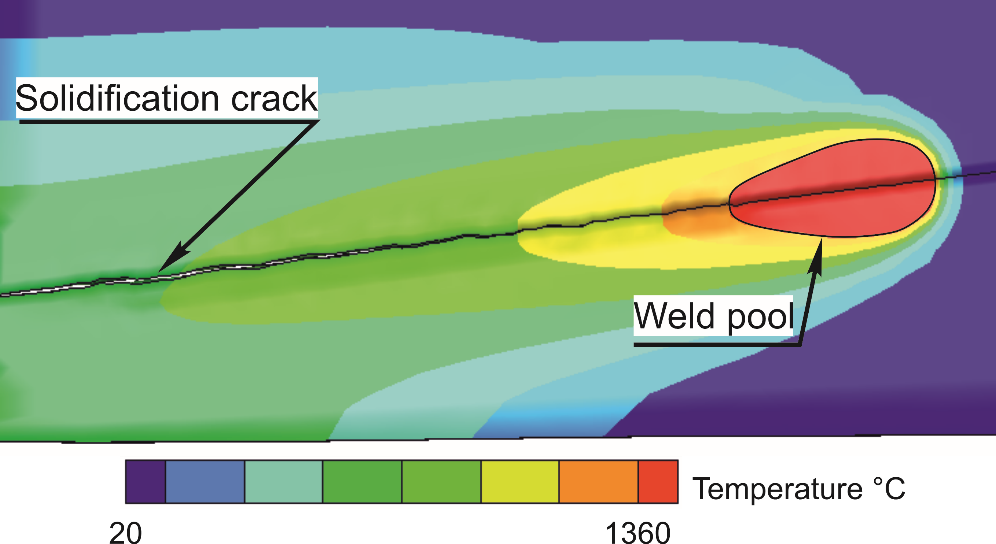
Work plan
The macromodel is constructed on the basis of a close-to-reality material model at meso level in the two-phase or multiphase domain. For this purpose, the developed viscoelastoplastic material laws from sub-project 4 will be implemented in the structural mechanical model. After the implementation of the temperature or phase dependent material laws and the equivalent heat source obtained from sub-project 2 into the macro model, a solidification cracking criterion will be developed taking into account the determined ductility capabilities of the material in the high temperature range. These will be further used to predict crack initiation and propagation.
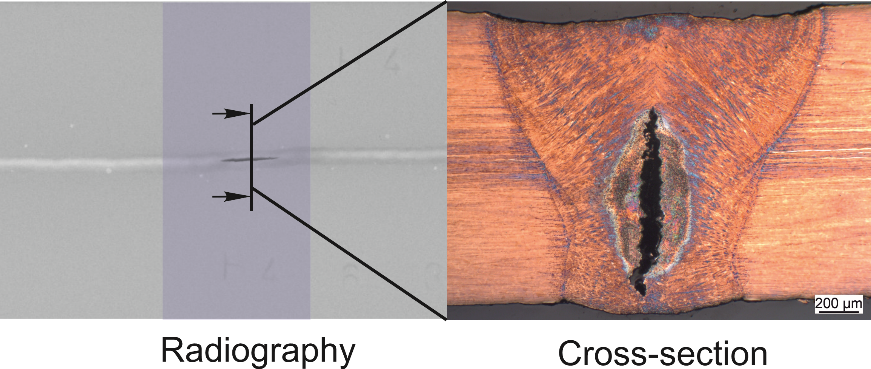
Another important task within the framework of SP1 is to conduct the necessary experiments and measurements to validate the numerical models, partly also for those at other subprojects. In addition, the local critical mechanical and thermal conditions responsible for solidification cracking will be determined with the help of an externally loaded hot cracking test in combination with an optical measurement technique.
Sub-project management
Prof. Dr.-Ing. Michael Rethmeier
Bundesanstalt für Materialforschung und –prüfung (BAM)
Welding Technology
- Email: michael.rethmeier@bam.de
Sub-project researcher
Habibi Naloufar
Bundesanstalt für Materialforschung und –prüfung (BAM)
Welding Technology
- Email: niloufar.habibi@bam.de
Dr.-Ing. Andrey Gumenyuk
Bundesanstalt für Materialforschung und –prüfung (BAM)
Welding Technology
- Email: andrey.gumenyuk@bam.de