Motivation
Durch die Zugabe von Legierungselementen können Stähle mit höheren Festigkeiten und besserer Umformbarkeit produziert werden. Damit einhergehend können Nachteile bezüglich der Schweißeignung oder Rissanfälligkeit entstehen. Um die komplexen thermomechanischen Vorgänge beim Laserstrahlschweißen im Bereich der Mischzone und des Erstarrungsbereiches, welche sich auf der Mikroskala abspielen, adäquat abzubilden und zu untersuchen und deren Auswirkung auf der Makroskala zu analysieren, bedarf es eines mehrskaligen Modellierungsansatzes. Die Herausforderungen sind dabei die Berücksichtigung der damit auftretenden multiphysikalischen und mehrskaligen Effekte und die Abbildung der zeitlich veränderlichen Mikrostruktur der Erstarrungszone. Für die Entwicklung einer effizienten Software zur Prozesssimulation ist die Zusammenarbeit von Mechanik und Mathematik unabdingbar. Auch werden Informationen zu metallurgischen Eigenschaften auf der Mikroskala benötigt, um ein aussagekräftiges Modell zu entwickeln. Dabei steht die Entwicklung einer hochskalierbaren Softwareumsetzung der FE2-Methode auf Basis der Kombination geeigneter Materialmodellierung sowie Lösungsverfahren im Fokus.
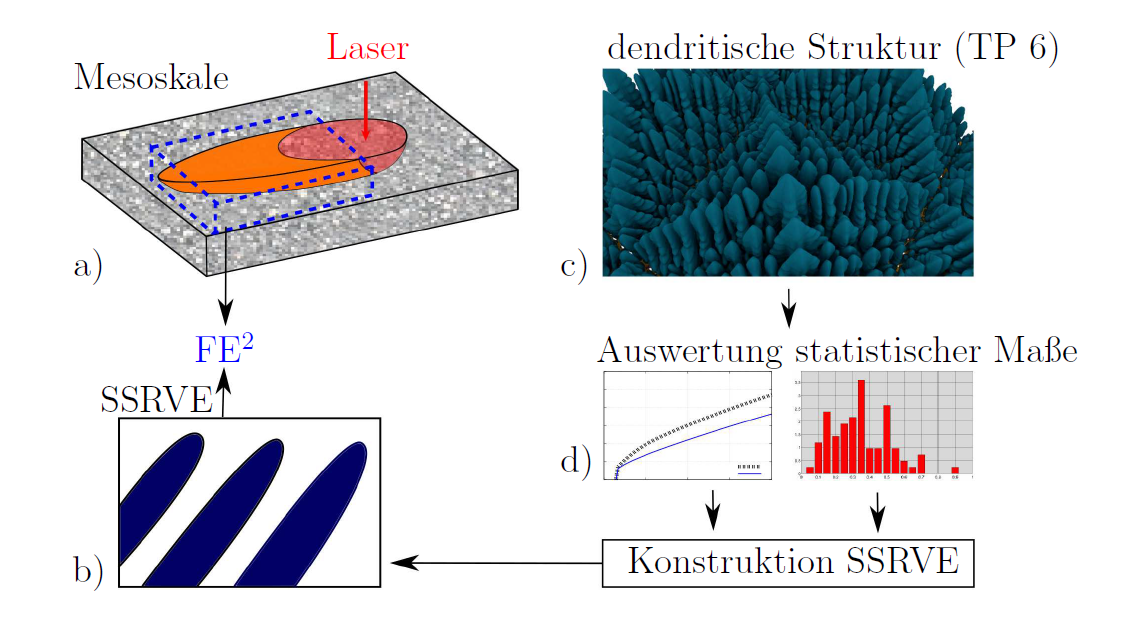
Ziel
Im Rahmen des Teilprojekts 4 (TP4) wird ein mehrskaliger thermomechanisch gekoppelter Modellierungsansatz für das Laserstrahlschweißen entwickelt. Die Betrachtung des Prozesses erfolgt einerseits auf der Mesoebene, die einen Teil der Makroebene im Bereich der Mischzone abbildet, und andererseits auf der Mikroebene, die die dendritische Mikrostruktur in der Erstarrungszone widerspiegelt. Die zweiskalige Betrachtung erfolgt mit der FE2-Methode. Das Ziel liegt dabei in der Bestimmung von Spannungs- und Dehnungsverteilungen, die für die Erstarrungsrissentstehung eine entscheidende Rolle spielen. Um mikrostrukturelle Effekte effizient zu simulieren, wird die Mikrostruktur über ein statistisch ähnlich relevantes Volumenelement (SSRVE) abgebildet. Da sowohl Prozessführung als auch der betrachtete Ort verschiedene Mikrostrukturvarianten hervorbringen, werden diese jeweils auf ihre Rissempfindlichkeit hin analysiert und bewertet.
Vorgehensweise
Zur Prozesssimulation des Laserstrahlschweißens wird in TP4 zunächst ein Wärmequellenmodell implementiert, welches im ersten Schritt mit experimentellen Daten aus Teilprojekt 1 und Teilprojekt 2 kalibriert wird. Im Verlauf des Projekts wird zusätzlich eine Schnittstelle zur Einbindung des in Teilprojekt 3 entwickelten thermo-fluiddynamischen Schmelzbadmodells aufgebaut und implementiert. Die Materialmodellierung der flüssigen und der festen Phasenanteile der Mischzone erfolgt über eine thermodynamisch konsistente Formulierung im Rahmen der Thermoelastoplastizität. Das entwickelte Modell wird in engem Austausch mit Teilprojekt 5 in die Softwareumgebung zur Prozesssimulation implementiert und für erste Simulationsstudien auf Mikro- und Mesoebene genutzt. Zur Darstellung der dendritischen, veränderlichen Mikrostruktur in der Mischzone wird der Ansatz der SSRVEs erweitert. Als Grundlage dienen Daten aus der Literatur, die später durch hochaufgelöste Phasenfeldmodelle aus Teilprojekt 6 ersetzt werden. Der Einbau in die Softwareumgebung zur Multiskalensimulation des Laserstrahlschweißprozesses wird wiederum in enger Abstimmung mit Teilprojekt 5 erfolgen. Die so entwickelte Software liefert abhängig von der Prozessführung Aussagen zu Spannungs- und Dehnungszuständen im Material und kann in Studien zur Abschätzung von Rissanfälligkeit eingesetzt werden.
Teilprojektleitung
Jun.-Prof. Dr.-Ing. Lisa Scheunemann
RPTU Kaiserslautern-Landau
Lehrstuhl für Technische Mechanik (LTM)
- E-Mail: lisa.scheunemann@rptu.de
Prof. Dr.-Ing. Jörg Schröder
Universität Duisburg-Essen (UDE)
Institut für Mechanik (IfM)
- E-Mail: j.schroeder@uni-due.de
Teilprojektbearbeitung
Philipp Hartwig, M.Sc.
Universität Duisburg-Essen (UDE)
Institut für Mechanik (IfM)
- E-Mail: philipp.hartwig.ph97@uni-due.de